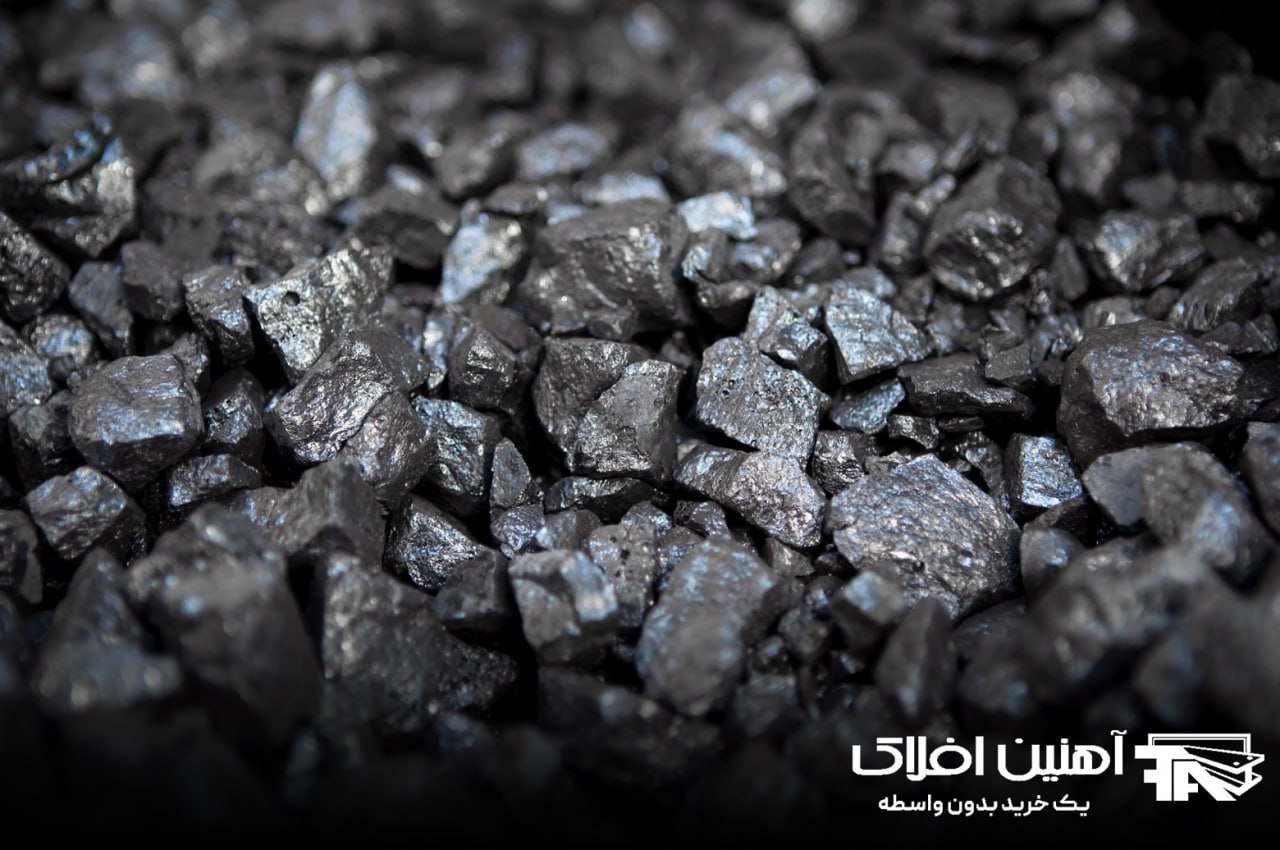
سنگ آهن چیست
سنگ آهن، عنصری ارزشمند، در پوسته زمین یافت میشود و ماده اولیه ضروری برای تولید فولاد است. پس از استخراج از معدن، این سنگ خام به تنهایی به دلیل ناخالصیها استحکام کافی ندارد. برای غلبه بر این مشکل، کروم و نیکل به آن اضافه میشود تا استحکام و کیفیت فلز را افزایش دهد. محصول نهایی، فولاد، سپس در طیف گستردهای از صنایع از جمله ساخت و ساز، لوازم خانگی و خودرو کاربرد دارد.
با افزایش تقاضا برای فولاد، قیمت سنگ آهن نیز به طور قابل توجهی افزایش یافته است. این امر برخی از تولیدکنندگان را بر آن داشته تا به جای فولاد، از آلومینیوم به عنوان جایگزین کمهزینهتر در تولید محصولات خود استفاده کنند.
کاربردهای سنگ آهن
سنگ آهن، ماده اولیه تولید فولاد، نقش حیاتی در دنیای مدرن ایفا میکند. کاربرد اصلی آن در صنایع مختلف از جمله لوازم خانگی، خودروسازی، ساخت و ساز و راه آهن مشهود است. اما کاربردهای سنگ آهن فراتر از فولاد است. سولفات آهن به عنوان قارچ کش، اگزالات آهن در عکاسی، لیمونیت، گوتیت و هماتیت به عنوان رنگدانه و ساینده، و مگنتیت در الکترودهای صنعتی و تصفیه زغال سنگ کاربرد دارند. کلرید و نیترات آهن در خشک کردن و تولید جوهر، کربونیل آهن به عنوان کاتالیزور و هماتیت میکاسی به عنوان رنگ محافظ روی فولاد استفاده میشوند. به طور خلاصه، سنگ آهن مادهای ارزشمند با کاربردهای گسترده در صنایع مختلف است.
منابع جهانی سنگ آهن
ذخایر جهانی سنگ آهن خام بسیار عظیم است و تخمین زده میشود که بیش از 800 میلیارد تن سنگ آهن خام حاوی بیش از 230 میلیارد تن آهن وجود داشته باشد. در حال حاضر، استخراج سنگ آهن عمدتاً از معادن با عیار بالا انجام میشود که از سنگهای هماتیت عظیم یا گوتیت پیزولیتی تشکیل شدهاند. چین، استرالیا و برزیل بزرگترین تولیدکنندگان سنگ آهن در جهان هستند و در سال 2013، تولید جهانی به 2.95 میلیارد تن رسید. استرالیا با تولید 530 میلیون تن در این سال، پیشرو در تولید این ماده معدنی بود. در استرالیای جنوبی، 12 میلیون تن سنگ آهن، شامل 3.2 میلیون تن سنگ معدن، در سال 2013 استخراج شد.
استخراج و خالصسازی آهن از دل سنگ
آهن، عنصری ارزشمند که در دنیای امروز کاربردهای فراوانی دارد، به طور طبیعی در سنگ آهن یافت میشود. اما برای استفاده از آن، باید فرآیندی برای خالصسازی و جداسازی آهن از ناخالصیها طی شود. این فرآیند شامل مراحل مختلفی از جمله خرد کردن، آسیاب کردن، سرند کردن و شستشو با استفاده از روشهای نوین مانند جداسازی مغناطیسی یا فلوتاسیون است.
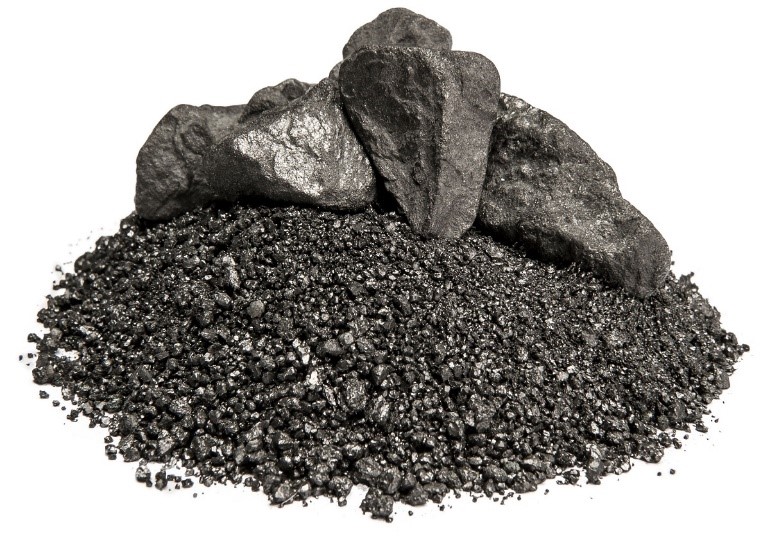
مراحل فرآوری سنگ آهن چیست؟
سنگ آهن پس از استخراج از معدن، ناخالصیها و ترکیبات مضر دارد و عیار آن پایین است. به همین دلیل برای خالصسازی و افزایش عیار، سنگ آهن طی فرآیندی به نام فرآوری، مراحل مختلفی را پشت سر میگذارد.
1- غربالگری
در غربالگری ذرات ریز از سنگ جدا میشود. این کار با استفاده از صفحههای استاتیک انجام شده و به افزایش کارایی مراحل بعدی، به خصوص خرد کردن، کمک میکند.
سپس سنگ آهن فرآوری میشود تا ناخالصیها از آن جدا شده و عیار آن افزایش یابد. این فرآوری میتواند به روشهای مختلفی مانند کنسانتره سازی، گندله سازی و دانهبندی انجام شود.
در نهایت، محصول نهایی با توجه به نیاز مصرف کنندگان به اشکال مختلفی در اختیار آنها قرار میگیرد.
2-تولید سنگ آهن دانه بندی شده
در فرآیند تولید سنگ آهن دانهبندی شده، از روشی خشک و بدون استفاده از آب بهره برده میشود. این نوع سنگ آهن به دلیل عیار پایینتر، در کورههای بلند کاربرد دارد.
3.تولید کنستانتره
تولید کنسانتره سنگ آهن، فرایندی وابسته به آب است که با غنیسازی عیار سنگ آهن، کاربردهای متنوعی را برای آن به ارمغان میآورد. این فرآیند شامل مراحل خرد کردن، آسیاب کردن، پرعیارسازی و آبگیری میشود. اهمیت فرآوری سنگ آهن در تولید فولاد باکیفیت و اقتصادی خلاصه میشود. این فرآیند نه تنها هزینههای تولید فولاد را به طور قابل توجهی کاهش میدهد، بلکه با تصفیه بهتر، آلودگی کمتری نیز به همراه دارد.
سنگ آهن فرآوری شده در بازار به اشکال مختلفی عرضه میشود که از جمله آنها میتوان به سنگ آهن دانهبندی شده (با احیایپذیری پایینتر)، سنگ و کلوخ (پرمصرف در صنایع فولاد) و گندله (محصولی از نرمه سنگ آهن و افزودنیها که کاربرد آن در کوره بلند و احیای مستقیم است) اشاره کرد.
در واقع، فرآوری سنگ آهن نقش اساسی در زنجیره تولید فولاد ایفا میکند و با ارتقای کیفیت و کاهش هزینهها، به پویایی و رونق این صنعت کمک شایانی مینماید.
معادن سنگ آهن ایران
ایران دارای معادن متعدد سنگ آهن است که به طور فعال مورد بهره برداری قرار میگیرند. معدن چغارت در بافق یزد، به عنوان اولین معدن سنگ آهن ایران، با دارا بودن یک سوم از ذخایر آهن کشور، بزرگترین و مهمترین منطقه آهنی ایران محسوب میشود. شرکت ذوب آهن اصفهان از جمله مشتریان اولیه این معدن بوده است. با وجود سابقه طولانی، ذخایر این معدن رو به اتمام است. در حال حاضر، عنوان بزرگترین معدن سنگ آهن ایران به معدن چادرملو اختصاص یافته و معادن گل گهر، فولاد صبا نور و سنگان نیز از دیگر معادن مهم سنگ آهن کشور هستند.
عوامل موثر بر قیمت سنگ آهن در جهان و ایران
قیمت سنگ آهن در بازار جهانی تحت تاثیر عوامل متعددی از جمله قیمت فولاد، شاخص تولید ناخالص داخلی، قیمت نفت خام، قیمت آلومینیوم، قیمت طلا، نرخ بهره، نرخ تورم، ارزش دلار، ارزش سهام و میزان تولید آهن و فولاد قرار دارد. در ایران، از سال 1380 به دلیل دولتی بودن زنجیره فولاد، قیمت سنگ آهن به صورت دستوری تعیین می شد. با افزایش صادرات سنگ آهن به چین و فعالیت معادن خصوصی، اختلاف قیمت بین بازار داخلی و صادرات مطرح شد و تلاش هایی برای رفع این اختلاف انجام شد.
کارشناسان معتقدند که مهمترین عوامل موثر بر قیمت سنگ آهن در ایران عبارتند از:
- قیمت دلار
- میزان عرضه و تقاضا
- نرخ ارز
- شیوه قیمت گذاری شرکت های بزرگ
در ادامه به توضیح مختصری درباره ای موارد گفته شد خواهیم پرداخت:
عرضه و تقاضا
نوسانات عرضه و تقاضا در بازار داخلی، به طور مستقیم بر قیمت نهایی آهن تاثیر میگذارد. زمانی که تقاضا برای آهن افزایش یابد و عرضه به اندازه کافی نباشد، قیمتها بالا میروند. برعکس، زمانی که عرضه از تقاضا پیشی میگیرد، قیمتها به سمت پایین حرکت میکنند.
تاثیر قیمت فولاد بر قیمت سنگ آهن
قیمت سنگ آهن، به عنوان ماده اولیه تولید فولاد، تحت تاثیر عوامل مختلفی از جمله قیمت فولاد قرار میگیرد. در گذشته، قیمت سنگ آهن عمدتاً از طریق مذاکره بین شرکتهای معدنی بزرگ و فولادسازان تعیین میشد و به عنوان شاخصی برای قیمت صنعت فولاد عمل میکرد.
علاوه بر این، هرگونه نوسان در قیمت سنگ آهن، به عنوان ماده اولیه تولید مقاطع فولادی، بر قیمت نهایی محصولاتی مانند میلگرد و تیرآهن تاثیرگذار خواهد بود. نکته قابل توجه این است که تولیدکنندگانی که از سنگ آهن برای تولید مقاطع فولادی استفاده میکنند، به دلیل پایینتر بودن قیمت تمام شده محصول، نسبت به تولیدکنندگانی که از قراضه استفاده میکنند، از مزیت اقتصادی برخوردار هستند.
قیمت دلار
قیمت نهایی سنگ آهن تحت تاثیر شاخصهای نرخ بین المللی که به دلار آمریکا تعیین میشوند، قرار دارد. به همین دلیل، نوسانات نرخ ارز، به طور مستقیم قیمت سنگ آهن را تحت تاثیر قرار میدهد.
با این حال، این نوسانات میتوانند پیامدهای مثبتی هم داشته باشند. برخی کارشناسان بر این باورند که افزایش همزمان قیمت سنگ آهن و نرخ دلار در ایران، باعث رونق کسب و کار معادن کوچک سنگ آهن شده و به احیای فعالیت آنها کمک کرده است.
تولید و قیمت گذاری شرکت های معدنی بزرگ
استرالیا، چین و برزیل به عنوان غولهای تولید سنگ آهن در جهان شناخته میشوند، در حالی که روسیه و آمریکا نیز سهم قابل توجهی در این بازار دارند. استرالیا در صادرات سنگ آهن پیشرو بوده، اما چین به دلیل تقاضای داخلی بالا، بیشتر تولیدات خود را در صنایع فولادی خود مصرف میکند. قیمتگذاری و تولید در این بازار تحتتأثیر فعالیتهای این کشورها قرار دارد. در سالهای اخیر، شاهد تغییر از نرخگذاری سالانه به قراردادهای کوتاهمدت بودهایم و بسیاری از معدنکاران بزرگ، بهویژه در استرالیا و برزیل، به دنبال توافقهای کوتاهمدت هستند.
پیش بینی قیمت سنگ آهن
قیمت جهانی سنگ آهن تحت تاثیر عوامل مختلفی قرار میگیرد که میتوان آنها را به دو دسته کلی عوامل کلان و عوامل خرد تقسیم کرد.
عوامل کلان شامل عواملی مانند موجودی بنادر در کشورهای صادرکننده و چین، موجودی انبارهای فولادسازان، شاخص حمل دریایی، قیمت فولاد، شاخصهای اقتصادی کلان چین، تولید ناخالص داخلی چین، قیمت طلا، قیمت نفت، نرخ بهره، نرخ تورم و ارزش دلار میشود.
رشد موجودی بنادر، موجودی انبارها و یا شاخصهای اقتصادی کلان چین، قیمت سنگ آهن را کاهش میدهد، در حالی که رشد شاخص حمل دریایی، قیمت فولاد و یا پارامترهایی مانند تولید ناخالص داخلی چین، قیمت طلا و قیمت نفت، سبب افزایش قیمت سنگ آهن میشود.
عوامل خرد نیز شامل عواملی مانند بازگشت چینیها از تعطیلات، رسیدن موجودی انبارهای سنگ آهن به سطح خاصی، یا خبر بازگشت شرکتهای معدنی به فعالیت، میشود.به دلیل پیچیدگی روابط بین این عوامل، امروزه از روشهای هوش مصنوعی مانند شبکههای عصبی مصنوعی برای پیشبینی قیمت سنگ آهن استفاده میشود. بر اساس مطالعات انجام شده، پارامترهایی مانند تولید ناخالص داخلی چین، قیمت طلا و قیمت نفت، بیشترین تاثیر را بر قیمت سنگ آهن دارند، در حالی که پارامترهایی مانند نرخ بهره، نرخ تورم و ارزش دلار، کمترین تاثیر را بر آن میگذارند.
سخن پایانی
سنگ آهن، از جمله فلزات ارزشمند با کاربردهای گسترده در صنایع مختلف و حتی داروسازی، نقشی حیاتی در اقتصاد جهانی ایفا میکند. در حال حاضر، شاهد افزایش همزمان قیمت سنگ آهن، میلگرد و سایر محصولات فولادی هستیم. این امر ناشی از سیگنالهای مثبت در بخشهای عرضه و تقاضا است. در بخش عرضه، شرایط آب و هوایی و در بخش تقاضا، تقاضای بالای چین نقش کلیدی دارند. با این حال، افزایش قیمتها بدون ریسک نیست. چنانچه افزایش قیمت محصولات فولادی منجر به کاهش تقاضا شود، این امر میتواند بهطور ناخواسته بر قیمت سنگ آهن نیز اثر بگذارد. با وجود این چالشها، چشمانداز بلندمدت برای سنگ آهن و صنایع وابسته به آن روشن به نظر میرسد.
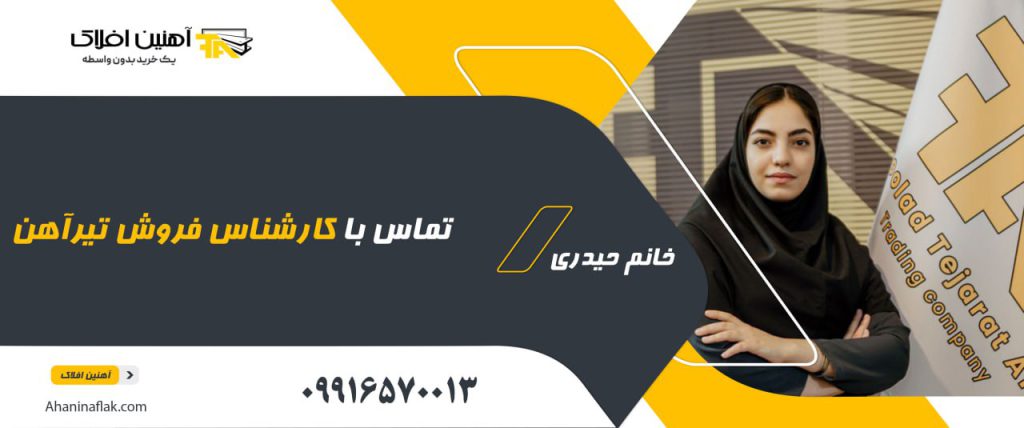