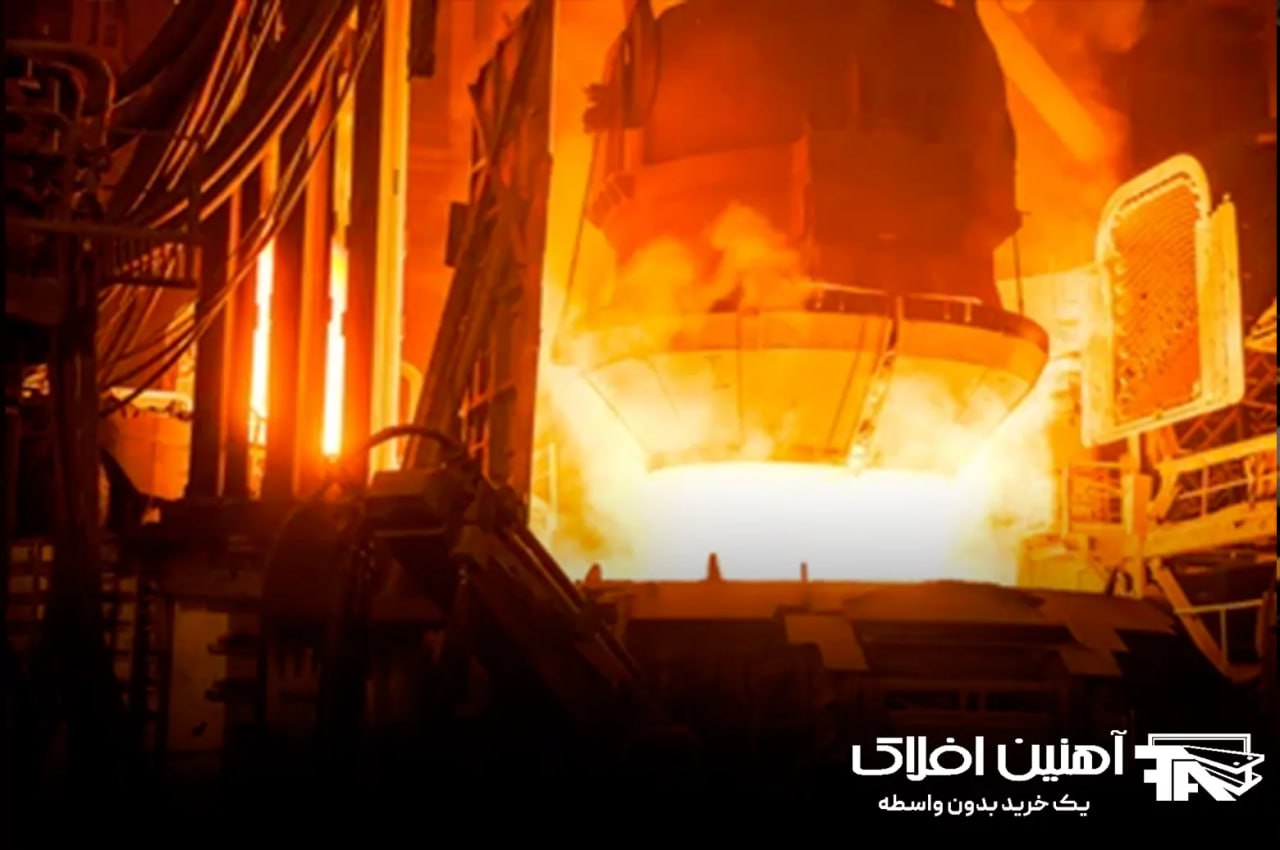
کوره قوس الکتریکی (EAF): قلب تپنده صنعت ذوب فلز
کوره قوس الکتریکی (EAF) که مخفف (Electric Arc Furnace) است با ایجاد حرارت بالا و نرخ تولید چشمگیر، به عنوان ابزار قدرتمندی در ذوب فلزات آهنی و غیرآهنی در صنایع مختلف، از جمله صنعت فولاد ایران و جهان شناخته میشود. این کوره که شامل ۸ واحد با ظرفیت ذوب ۱۸۰ تن فولاد در هر مرحله و مجهز به ترانسفورماتور ۹۰ مگاولت آمپر است، از قراضهها به عنوان ماده اولیه استفاده میکند. قراضهها توسط جرثقیل به داخل کوره منتقل و با ایجاد قوس الکتریکی ذوب میشوند. در ادامه این مقاله به بررسی تخصصیتر کوره قوس الکتریکی، انواع و کاربردهای آن میپردازیم.
کوره قوس الکتریکی چیست؟
کوره قوس الکتریکی ابزاری کارآمد و انعطافپذیر در فرآیند ذوب فلزات، به ویژه فولاد و چدن، است. این کورهها با استفاده از قوس الکتریکی و ایجاد حرارت بالا، مواد اولیه را ذوب میکنند و EAFها در اندازههای مختلفی ساخته میشوند. در ایران، دو نوع اصلی آن، شامل کورههای قوس الکتریکی سنتی (تخلیه از ناودان) و EBT (تخلیه از کف)، به طور گسترده مورد استفاده قرار میگیرند.
دمای ذوب و تخلیه در کورههای قوس الکتریکی به طور معمول در حدود 1600 درجه سانتیگراد است. با این حال، در برخی از کورههای آزمایشگاهی، این دما میتواند تا 3000 درجه سانتیگراد نیز افزایش یابد.
عملکرد کوره قوس الکتریکی بر پایه ذوب بار کوره توسط قوس الکتریکی ایجاد شده. بین الکترودهای گرافیتی و بار فلزی استوار است، در این روش، ابتدا آهن اسفنجی تولید شده در فرآیند احیای مستقیم، درون کوره قوس الکتریکی ریخته میشود تا فرآیند ذوب بر روی آن انجام گیرد. دمای بالای کوره منجر به تولید فولاد با درصد کربن نسبتاً پایین در همان ذوب اولیه میشود. سپس فولاد مذاب به درون کوره پاتیلی منتقل شده و فرآیند آلیاژسازی در آن انجام میشود. این فرآیند شامل تنظیم میزان کربن، اضافه کردن عناصر آلیاژی و یکدستسازی ترکیب شیمیایی فولاد نهایی است.

انواع کوره های (EAF)
1- کوره قوس الکتریکی AC:
این نوع کوره، رایجترین نوع کوره قوس الکتریکی است که از جریان متناوب (AC) برای ایجاد قوس الکتریکی و ذوب فلزات استفاده میکند. کورههای قوس الکتریکی AC به دو دسته تک الکترود و چند الکترود تقسیم میشوند.
کوره قوس الکتریکی AC تک الکترود: این کورهها برای ذوب فلاد در مقیاسهای کوچک و متوسط مناسب هستند و به دلیل سادگی طراحی و عملکرد، از محبوبیت بالایی برخوردارند.
کوره قوس الکتریکی AC چند الکترود: این کورهها از چند الکترود گرافیتی برای ذوب فلزات استفاده میکنند و به دلیل راندمان بالا و پایداری قوس، برای ذوب فلاد در مقیاسهای بزرگ مناسب هستند.
2- کوره قوس الکتریکی DC:
در این نوع کوره، از جریان مستقیم (DC) برای ایجاد قوس الکتریکی استفاده میشود. کورههای قوس الکتریکی DC به دلیل پایداری بیشتر قوس و کیفیت ذوب بالاتر، برای ذوب فلادهای خاص مانند فولاد ضد زنگ و آلیاژهای نیکل مورد استفاده قرار میگیرند.
3- کوره قوس الکتریکی با وکیوم:
در این نوع کوره، فرآیند ذوب در شرایط خلا انجام میشود. کورههای قوس الکتریکی با وکیوم به دلیل حذف گازهای مزاحم از مذاب، فلز با کیفیتتر و خالصتر تولید میکنند. این کورهها برای ذوب فلادهای خاص مانند فولاد ابزار و فولاد آلیاژی مورد استفاده قرار میگیرند.
4- کوره قوس الکتریکی با تاپ پات:
در این نوع کوره، ذوب فلز در یک ظرف جداگانه (تاپ پات) انجام میشود. کورههای قوس الکتریکی با تاپ پات به دلیل کنترل دقیق دمای ذوب و کیفیت بالای فلز تولیدی، برای ذوب فلادهای خاص مانند فولادهای دریایی و فولادهای هستهای مورد استفاده قرار میگیرند.
5- کوره قوس الکتریکی با القایی:
در این نوع کوره، از میدان مغناطیسی القایی برای ذوب فلز استفاده میشود. کورههای قوس الکتریکی با القایی به دلیل عدم آلودگی الکترود به مذاب و کیفیت بالای فلز تولیدی، برای ذوب فلادهای خاص مانند فولادهای پزشکی و فولادهای با گرید بالا مورد استفاده قرار میگیرند.
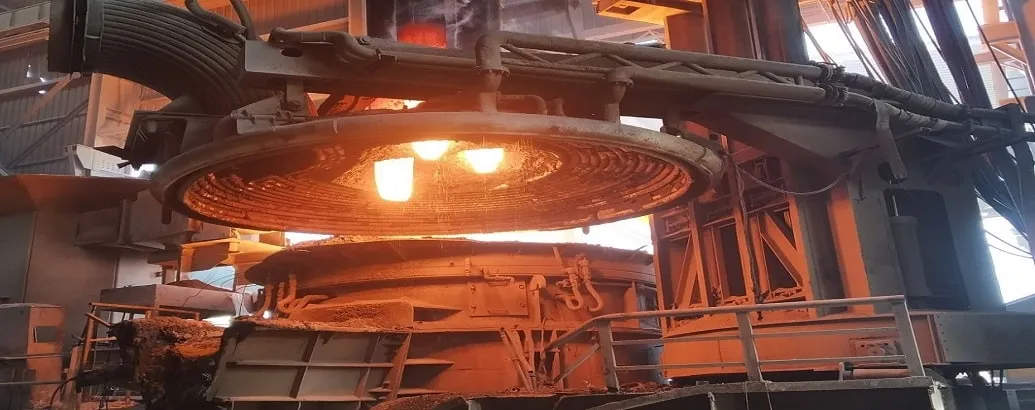
کاربرد کوره قوس الکتریکی (EAF)
کورههای قوس الکتریکی (EAF) کاربردهای فراوانی در صنایع مختلف دارند. ذوب طیف گستردهای از فولادها با گریدهای مختلف، تولید مقاطع فولادی مانند میلگرد و ناودانی، بازیافت ضایعات فلزی، ذوب فلزات غیرآهنی، ریختهگری و تصفیه فلزات، تنها نمونههایی از کاربردهای متنوع این کورههای قدرتمند هستند. انعطافپذیری بالا، راندمان، قابلیت ذوب ضایعات، کیفیت و سازگاری با محیط زیست، از جمله مزایای استفاده از کورههای قوس الکتریکی است که آنها را به انتخابی ایدهآل برای صنایع مختلف تبدیل کرده است.
چگونه فلزات در کورههای EAF ذوب میشوند؟
در کورههای قوس الکتریکی، حوضچهای از مذاب آهن وجود دارد که با عبور جریان برق از الکترودهای موجود در بالای آن یا داخل آن، به دمای ذوب میرسد. سه الکترود که هر کدام به یک فاز جریان برق متصل هستند، از سقف کوره عبور میکنند و با حرکت نوسانی خود، طول قوس الکتریکی و در نتیجه، حرارت مورد نیاز برای ذوب مواد را کنترل میکنند. پس از رسیدن دمای مذاب به 1550 درجه سانتیگراد، جرقه زده میشود و قراضهها ذوب میشوند. سپس، شارژ آهن اسفنجی به کوره آغاز شده و ولتاژ تا رسیدن به سطح مطلوب کاهش مییابد. این فرآیند پیچیده، رمز ذوب فلزات و تولید فولاد در کورههای قوس الکتریکی است.
نگاهی به اجزای اصلی کورههای قوس الکتریکی
1. سقف کوره: این بخش به مانند یک کلاهک، وظیفه محافظت از داخل کوره و هدایت دود و گازها را بر عهده دارد. سقف کوره به گونهای طراحی میشود که هم سبک باشد و هم استحکام لازم برای تحمل وزن الکترودها و فشار ناشی از قوس الکتریکی را داشته باشد. در سقف کورههای قوس الکتریکی معمولاً سه سوراخ تعبیه شده که محل عبور الکترودها هستند. همچنین، سقف برخی از کورهها به گونهای طراحی میشود که همراه با الکترودها قابل حرکت باشد.
2. دیوار جانبی کوره: این دیوارها که به صورت استوانهای هستند، وظیفه دارند تا از هدر رفتن حرارت از داخل کوره جلوگیری کنند. دیوارههای جانبی از مواد نسوز و همچنین لولههای آبگرد پوشیده میشوند تا در برابر حرارت بالا و خوردگی مقاوم باشند.
3. کف یا بوته کوره: بوته کوره که حالت قوسی شکل دارد، محل ذوب فلزات و انجام فرآیند ذوب است. عمق بوته نسبتاً کم و سطح آن زیاد طراحی میشود تا فصل مشترک مذاب با سرباره (مواد زائد ذوب) بیشترین میزان ممکن باشد. این امر به تسریع فرآیند ذوب و افزایش کیفیت فولاد تولیدی کمک میکند.
تجهیزات الکتریکی کورههای قوس الکتریکی
1. کلید قطع و وصل مدار: این کلید وظیفه دارد تا جریان برق را به کوره هدایت کرده و در صورت نیاز، آن را قطع کند.
2. راکتور و ترانسفورماتور: این دو بخش وظیفه دارند تا ولتاژ و جریان برق را به مقادیر مورد نیاز برای ایجاد قوس الکتریکی در کوره تنظیم کنند.
3. تنظیم کنندههای الکترود: این تنظیم کنندهها وظیفه دارند تا ارتفاع الکترودها را در داخل کوره به طور دقیق کنترل کنند.
الکترودها در کوره قوس الکتریکی (EAF)
الکترودها، به عنوان یکی از اجزای اصلی کورههای قوس الکتریکی، نقشی حیاتی در انتقال جریان الکتریکی از بازوهای الکترود به بار کوره و ایجاد قوس الکتریکی ایفا میکنند. این قوس الکتریکی، حرارت لازم برای ذوب فلزات و انجام فرآیند ذوب را فراهم میکند.
الکترودهای گرافیتی و زغالی از جمله مهمترین مواد مصرفی در کورههای قوس الکتریکی هستند. کیفیت این الکترودها تأثیر بسزایی در کیفیت مذاب و محصول نهایی دارد و از نظر اقتصادی نیز سهم قابل توجهی از هزینههای تولید را به خود اختصاص میدهند. انتخاب الکترود مناسب با خواص مشخص، شرط لازم برای تولید مذاب باکیفیت است.
یک الکترود باکیفیت باید دارای ویژگیهای زیر باشد:
هدایت الکتریکی بالا: برای انتقال efficient جریان الکتریکی و ایجاد قوس الکتریکی پایدار
مقاومت مکانیکی بالا: برای تحمل وزن خود و فشار ناشی از قوس الکتریکی
حاوی حداقل مواد مضر: برای جلوگیری از آلودگی مذاب و حفظ کیفیت محصول
مقاومت در برابر اکسایش: برای جلوگیری از تخریب الکترود در دمای بالا و افزایش طول عمر آن
قیمت مناسب: برای صرفه اقتصادی و کاهش هزینههای تولید
نگاهی به عملیات کوره قوس الکتریکی
کورههای قوس الکتریکی، ضایعات فلزی را به فولادی ارزشمند تبدیل میکنند. این فرآیند شگفتانگیز با ورود ضایعات فولاد از سه منبع اصلی (ضایعات خانگی، ضایعات صنعتی و ضایعات کهنه) به کوره آغاز میشود.
کوره قوس الکتریکی، غول پیکر صنعت فولاد، از یک حمام دوار با سقف متحرک تشکیل شده است که میزبان سه الکترود گرافیتی غولپیکر با ابعاد 6 متر طول و 4 متر عرض است. این کورههای عظیم، توانایی جای دادن تا 1000 تن فولاد را دارند.
پس از ورود ضایعات به کوره، سقف متحرک بسته شده و الکترودها در جای خود قرار میگیرند. قوس الکتریکی، رقصی از نور و گرما، با عبور جریان الکتریکی از طریق فلز آغاز میشود. گرمای حاصل از این قوس، ضایعات را ذوب کرده و آنها را به حوضچهای از مذاب تبدیل میکند.
برای تکمیل فرآیند ذوب و تولید فولاد با کیفیت، مواد زیر به کوره اضافه میشوند:
آهک: به شکل کلسیم اکسید یا کلسیم کربنات، برای خنثی کردن اسیدها و ناخالصیهای موجود در مذاب
فلورسپار (کلسیم فلوراید): برای مایع نگه داشتن سرباره (مواد زائد ذوب) و تسهیل جداسازی آن از فولاد
سنگ آهن: برای افزایش محتوای آهن در مذاب و ارتقای کیفیت فولاد
هنگامی که ترکیب مورد نظر استیل حاصل شد، سرباره از کوره خارج شده و فولاد خالص در کوره باقی میماند. با تخلیه کوره، به این فولاد ارزشمند دسترسی پیدا میشود. در گامی دیگر، سرباره نیز بازیافت شده و از آن آهن استخراج میشود.
مراحل شارژ کوره قوس الکتریکی
در کورههای قوس الکتریکی، ضایعات فولاد به عنوان ماده اولیه اصلی، نقشی حیاتی در صنعت فولاد ایفا میکنند. فراوانی، قیمت پایین و کیفیت مناسب ضایعات، از اهمیت ویژهای برخوردار است.
کیفیت ضایعات به خصوص در تولید فولاد با قابلیت نرم شدن بالا، نقشی کلیدی دارد. در این نوع فولاد، درصد کل عناصر ناخواسته (مس، کروم، نیکل، مولیبدن و قلع) باید حداکثر 0.2 درصد باشد.
متاسفانه، ضایعات اغلب حاوی این عناصر ناخواسته هستند که در فرآیند تولید فولاد اکسید نشده و در ضایعات بازیافتی تجمع مییابند. برای غلبه بر این مشکل، برخی از تولیدکنندگان ضایعات خود را با آهن مستقیماً احیا شده یا آهن کوره بلند سرد که عاری از ناخالصی هستند، ترکیب میکنند. به طور کلی، مقادیر زیاد کربن، نیتروژن و عناصر ناخواسته، فرآیند قوس الکتریکی را برای تولید فولادهای کم کربن و نرم مناسب نمیکند.
فروشندگان ضایعات فولاد ضد زنگ، معمولاً گریدهای مختلف را از یکدیگر جدا میکنند تا از اختلاط ناخواسته عناصر جلوگیری کنند. در مقابل، فروشگاههای فولاد پرآلیاژ مانند تولیدکنندگان فولاد ضدزنگ، ضایعات با ترکیب شیمیایی مشابه را تجمیع میکنند تا از افزودنیهای آلیاژی گرانقیمت در فرآیند تولید فولاد خود بکاهند.
گذری بر روشهای ذوب و جداسازی فلزات
در کورههای قوس الکتریکی، دو روش اصلی برای تصفیه، ذوب و جداسازی فلزات وجود دارد: روش اسیدی و روش بازی.
روش اسیدی:
این روش برای جداسازی گوگرد و فسفر از مواد اولیه مناسب نیست.
به همین دلیل، مواد اولیه باید کمترین میزان این عناصر را داشته باشند.
مزایای این روش شامل تامین مواد نسوز با هزینه کم، مصرف انرژی پایین، سیالیت بیشتر مذاب، روان بودن کمتر سرباره و داشتن آسترهای با دوام بالا است.
روش بازی:
این روش که روشی سادهتر و رایجتر است، امکان جداسازی فسفر و گوگرد تا حد قابل قبولی را فراهم میکند.
در این روش، آهک و فلوئوراسپار به شارژ کوره اضافه میشوند تا به عنوان مواد احیا کننده عمل کنند و ناخالصیها را از مذاب جدا کنند.
مزایا و معایب کوره قوس الکتریکی (EAF)
کورههای قوس الکتریکی به عنوان یکی از روشهای اصلی ذوب فولاد، جایگاه ویژهای در صنعت فولاد دارند. با این حال، مانند هر فرآیندی، مزایا و معایبی را نیز به همراه دارند.
معایب:
وابستگی به کیفیت قراضه: کیفیت فولاد تولیدی در این کورهها به طور قابل توجهی به کیفیت قراضه ورودی بستگی دارد. انتخاب نامناسب قراضه میتواند منجر به شکستن الکترودها، سرریز شدن فولاد مذاب و افزایش ضایعات شود.
مدت زمان ذوب طولانی: ذوب فولاد در کورههای قوس الکتریکی به زمان نسبتاً طولانیتری نیاز دارد که این امر به نوبه خود، مصرف برق را افزایش میدهد.
افزایش ناخالصیها: فرآیند ذوب در کوره قوس الکتریکی، به طور ذاتی، ناخالصیهای بیشتری را به فولاد نهایی وارد میکند.
مزایا:
استفاده از قراضه: مزیت اصلی این کورهها، استفاده از قراضه به عنوان ماده اولیه است. این امر بازیافت فولاد را تسهیل میکند، بهینهسازی مصرف منابع را به ارمغان میآورد و ضایعات را به حداقل میرساند.
انعطافپذیری: کورههای قوس الکتریکی از نظر توان عملیاتی، انعطافپذیری بالایی دارند و میتوان از آنها برای ذوب مقادیر کم فولاد نیز استفاده کرد. این امر آنها را برای تولیدکنندگان کوچک و کارگاههای تخصصی مناسب میسازد.