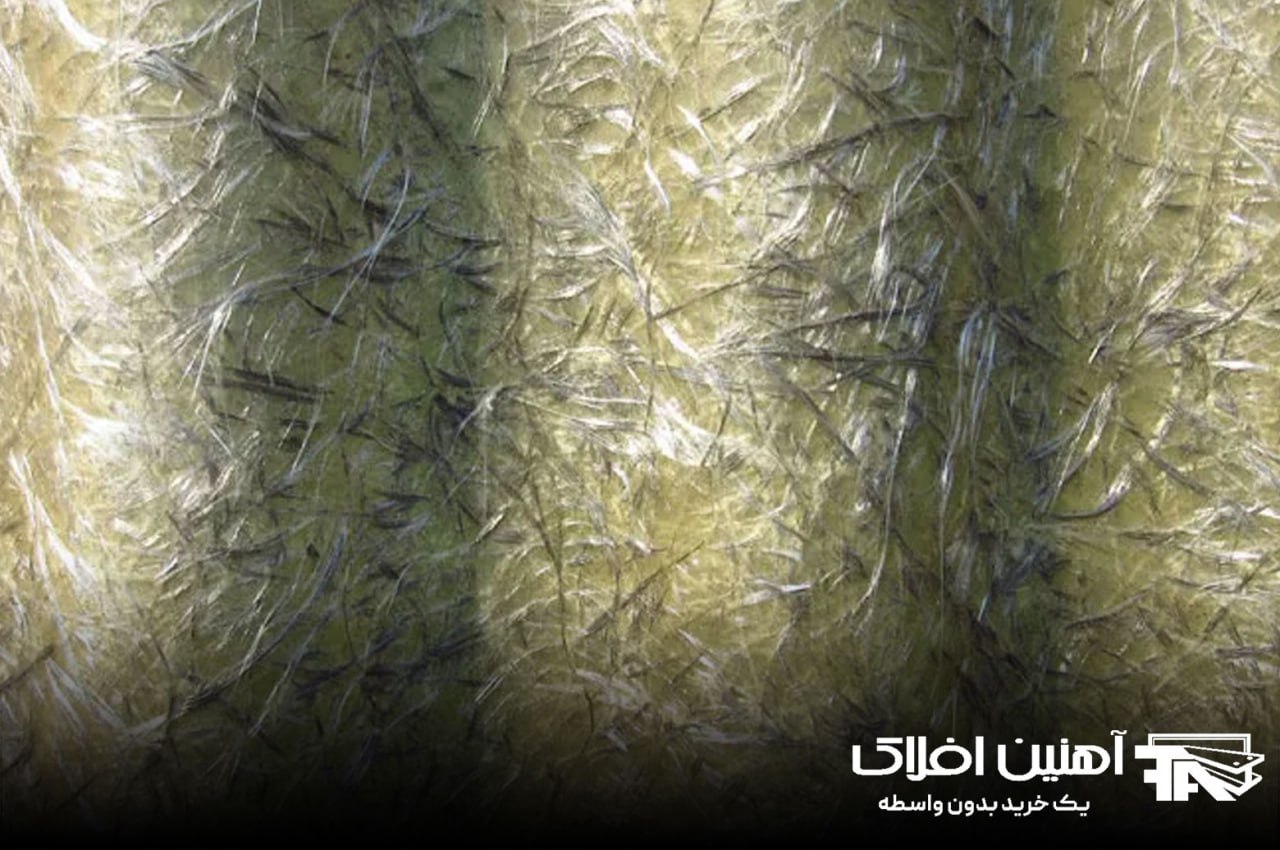
کامپوزیت چیست
کامپوزیت ها، ترکیبی از دو یا چند ماده با خواص فیزیکی و شیمیایی مجزا هستند که برای دستیابی به ویژگیهای دلخواه مانند استحکام، زیبایی یا مقاومت الکتریکی، با یکدیگر ترکیب میشوند. این مواد که در طبیعت (مانند چوب) و توسط بشر (از 1500 سال قبل از میلاد) به کار رفتهاند، به دلیل تنوع و مزایای فراوان، جایگاه ویژهای در صنایع مختلف پیدا کردهاند.
یکی از چالشهای فعلی، محدودیت تولید برخی کامپوزیتها مانند پروفیلها و بالا بودن قیمت آنها در ایران است. با این حال، به دلیل کاربردهای گسترده در ساخت میلگرد، قوطی، ناودانی و نبشی، تقاضا برای این مواد در بازار جهانی بالا است. انتظار میرود با افزایش تولید داخلی، قیمت کامپوزیتها در ایران نیز کاهش یابد.
نکته قابل توجه در مورد کامپوزیتها این است که مواد تشکیل دهنده آنها در یکدیگر حل نمیشوند و این امر منجر به بهبود خواصی مانند طول عمر و سختی میشود. از پلیاتیلن بدون رنگ در ساخت چمن مصنوعی استفاده میشود که به دلیل مات بودن، ظاهر زیبایی ندارد. برای حل این مشکل، وینیل استات به این پلیمر اضافه میشود تا خاصیت رنگپذیری و انعطافپذیری آن را افزایش دهد.
به طور کلی، هدف از تولید کامپوزیت، دستیابی به مادهای با خواص دلخواه است که از ترکیب مواد مختلف به دست میآید. این مواد کاربردهای گستردهای در صنایع مختلف دارند و انتظار میرود در آینده شاهد رشد و توسعه روزافزون آنها باشیم.
تفاوتهای بین آلیاژ و کامپوزیت:
درست است که هم آلیاژ و هم کامپوزیت از ترکیب دو یا چند ماده تشکیل شدهاند، اما تفاوتهای ساختاری و عملکردی آنها، کاربردهایشان را به طور قابل توجهی تفکیک میکند.
در ادامه به برخی از تفاوتهای کلیدی بین آلیاژها و کامپوزیتها اشاره میکنیم:
1- تعریف و ویژگیها
آلیاژها و کامپوزیتها هر دو از مخلوط چند ماده تشکیل میشوند، اما تفاوتهای اساسی در ساختار و خواص آنها وجود دارد. آلیاژها از ترکیب حداقل یک فلز با عناصر دیگر به دست میآیند، در حالی که در کامپوزیتها الزامی برای وجود فلز نیست و مواد میتوانند فلزی یا غیرفلزی باشند.
در آلیاژها، عناصر با یکدیگر واکنش شیمیایی میدهند و ساختاری یکپارچه ایجاد میکنند، در حالی که در کامپوزیتها، مواد به صورت جداگانه باقی میمانند و از طریق چسب یا ماتریس به یکدیگر متصل میشوند. این تفاوت در ساختار منجر به تفاوت در خواص نیز میشود. آلیاژها معمولاً خواص فیزیکی فلز پایه را حفظ میکنند، اما با بهبود مقاومت، سختی، هدایت الکتریکی و سایر ویژگیها، آنها را ارتقا میبخشند. در مقابل، کامپوزیتها میتوانند خواص کاملاً جدیدی با ترکیب ویژگیهای مواد تشکیلدهنده خود داشته باشند، مانند چگالی کم، استحکام بالا یا مقاومت در برابر حرارت. به طور خلاصه، آلیاژها فلزات ارتقا یافته هستند، در حالی که کامپوزیتها مواد جدیدی با خواص منحصر به فرد هستند
2- نوع مخلوط
آلیاژها مخلوطی از دو یا چند فلز (و گاه غیرفلز) هستند که میتوانند به دو دسته همگن و ناهمگن تقسیم شوند. دستهبندی آلیاژ بر اساس تعداد فازهای موجود در ساختار آن پس از ترکیب فلزات با یکدیگر صورت میگیرد. آلیاژی که فقط یک فاز داشته باشد، همگن و در غیر این صورت، ناهمگن در نظر گرفته میشود. در مقابل، تمام کامپوزیتها، صرف نظر از نوع عناصر تشکیلدهنده، ناهمگن هستند.
3- هدایت الکتریکی و درخشندگی
بر خلاف آلیاژها که به واسطه وجود فلز در ساختارشان، هادیهای جریان الکتریکی و براق هستند، در میان انواع کامپوزیتها، هیچکدام خاصیت درخشندگی را نداشته و تنها پلیمرها تا حدی قابلیت عبور جریان الکتریسیته را دارند، در حالی که سایر انواع کامپوزیت عایق هستند.
4- آرایش
کامپوزیتها همیشه دارای پیوند بین اجزای تشکیلدهنده خود هستند، چه پیوند شیمیایی و چه پیوند فیزیکی. این پیوندها باعث میشوند که کامپوزیتها به عنوان یک ماده واحد عمل کنند و خواص جدیدی را از خود نشان دهند که از اجزای تشکیلدهنده مجزا آنها متفاوت است.
از سوی دیگر، آلیاژها میتوانند بدون هیچ پیوندی بین اتمهای تشکیلدهنده خود وجود داشته باشند. در این حالت، آلیاژها به صورت مخلوطی از فلزات مختلف باقی میمانند که خواص هر یک از فلزات را به طور جداگانه حفظ میکنند.
5- نقاط ذوب و جوش
برخلاف آلیاژها که دمای ذوب و جوششان در ترکیبات مختلف متفاوت است، کامپوزیتها در دماهای مشخصی ذوب و جوش میآیند. این تفاوت به دلیل ماهیت تشکیلدهنده این دو ماده است.
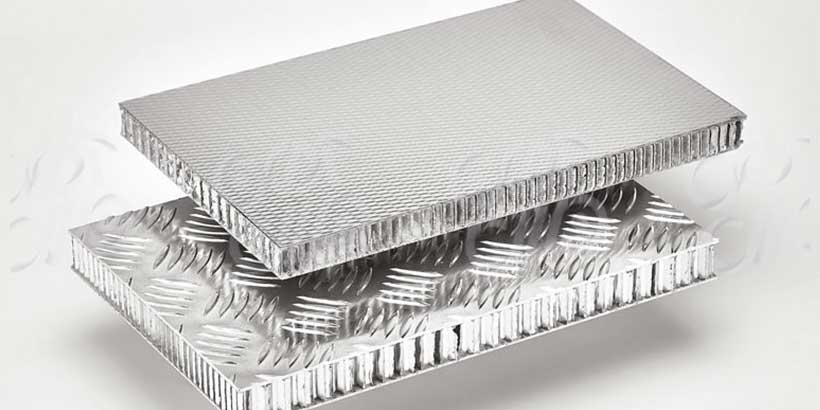
بررسی ساختار کامپوزیتها
نرخ کامپوزیتها به اجزای تشکیلدهنده آنها بستگی دارد. این مواد به طور کلی از سه بخش تشکیل شدهاند: ماتریس، تقویت کننده و فاز میانی که در ادامه به توضیح در مورد انها خواهیم پرداخت.
تقویت کننده ها به عنوان فاز ناپیوسته یا پراکنده در مواد کامپوزیتی، در اشکال مختلف الیاف، پوسته و ذرات با خواص متنوع حضور دارند. متداول ترین نوع آنها، الیاف هستند که به دلیل نسبت بالای طول به قطر، بیشترین تاثیر را بر ویژگی های مکانیکی کامپوزیت می گذارند. این امر سبب ایجاد تنش برشی موثری بین الیاف و ماتریس شده و قابلیت های پردازش و تولید قطعات کامپوزیتی در اشکال مختلف را افزایش می دهد. از جمله مهم ترین الیاف کامپوزیتی می توان به شیشه، کربن و آرامید اشاره کرد.
ماتریس، ماده ای پیوسته در کامپوزیت است که وظیفه اتصال، ثابت نگه داشتن و محافظت از الیاف یا دیگر تقویت کننده ها را بر عهده دارد. این ماده، با قرار دادن تقویت کننده ها در موقعیت مناسب و جلوگیری از حرکت و تغییر شکل آنها، به استحکام و پایداری کامپوزیت کمک می کند. انتخاب نوع ماتریس، مانند پلی استر، اپوکسی یا فنول، با توجه به خواص مورد نظر برای کامپوزیت نهایی، مانند مقاومت در برابر خوردگی، الکتریسیته، حرارت و اشتعال، انجام می شود.
فاز میانی، لایهای فشرده از ماتریس است که در سطح تقویتکننده تشکیل میشود و درواقع واسطهای بین این دو ماده محسوب میشود. اگرچه برای ذرات پراکنده با ابعاد میکرومیلیمتر، اثر این لایه ناچیز است، اما نانوذرات با سطح وسیعترشان میتوانند بخش قابل توجهی از حجم کامپوزیت را اشغال کنند. در نتیجه، در کامپوزیتهای تقویتشده با نانوذرات پراکنده، فاز میانی نقشی کلیدی در تعیین خواص نهایی ایفا میکند. به واقع، بسیاری از ویژگیهای برجسته نانوکامپوزیتها، مانند مقاومت تسلیم، ریشه در این فاز میانی دارند.
انواع کامپوزیتها
کامپوزیتها را میتوان به صورت زیر دستهبندی کرد:
– بر اساس فاز تقویتکننده
– بر اساس نوع مادهی زمینه
با توجه به نوع ماتریس، کامپوزیتها عمدتا در چهار گروه جای میگیرند.
1- کامپوزیتهای با زمینه فلزی (MMC)
کامپوزیتهای با زمینه فلزی (MMC) به دلیل خواص منحصر به فردشان، جایگاه ویژهای در صنعت هوافضا پیدا کردهاند. این نوع کامپوزیتها از یک فلز کمچگالی مانند آلومینیوم به عنوان زمینه و از الیاف تقویتکنندهای مانند کربن، کاربید، سیلیکون یا سرامیک تشکیل شدهاند. این ترکیب، مزایای فلزات (مانند شکلپذیری و هدایت حرارتی) را با مزایای سرامیکها (مانند استحکام و سختی) به ارمغان میآورد و آنها را به مادهای ایدهآل برای ساخت قطعات مختلف هواپیما تبدیل میکند.
2- کامپوزیتهای زمینه سرامیکی (CMC)
کامپوزیتهای زمینه سرامیکی (CMC) از ساختاری منحصر به فرد بهره میبرند که در آن الیاف سرامیکی یا کربنی نقش استخوانبندی را ایفا میکنند و توسط ماتریس سرامیکی، مانند کاربید سیلیکون، احاطه شدهاند. این ساختار نوآورانه، مزایای فوقالعادهای به CMC میبخشد، از جمله استحکام و مقاومت بالا، سبکی وزن، تحملپذیری در برابر حرارتهای شدید و مقاومت در برابر خوردگی.
3- کامپوزیتهای با زمینهی پلیمری (PMC)
کامپوزیتهای با زمینهی پلیمری یا PMC، که به عنوان پلاستیکهای تقویتشده با الیاف (FRP) نیز شناخته میشوند، از الیاف کوتاه یا بلند درون یک ماتریس پلیمری آلی تشکیل شدهاند. در این نوع کامپوزیت، ماتریس وظیفهی پخش بار بین الیاف را بر عهده دارد و به همین دلیل، استحکام و سختی قابل توجهی به کامپوزیت نهایی میبخشد. فایبرگلاس، که در آن از شیشه به عنوان مادهی تقویتکننده استفاده میشود، یکی از رایجترین نمونههای PMC است.
4- کامپوزیتهای کربن/کربن (CC)
کامپوزیتهای کربن/کربن (CC) از فیبرهای کربن به عنوان تقویتکننده در ماتریس کربنی استفاده میکنند. این الیاف میتوانند به صورت تابیده شده یا بافته شده باشند و ساختار سهبعدی به کامپوزیت میدهند.
بر اساس نوع ماده تقویتکننده، کامپوزیتها عبارتند از:
1- کامپوزیتهای تقویتشده با الیاف (FRC):
در میان کامپوزیتها، نوعی که در آن فاز پراکنده به شکل رشته است، جایگاه ویژهای در صنعت و تکنولوژی دارد. این نوع از کامپوزیتها که به FRC معروف هستند، از الیاف تقویتکننده با قطرهای مختلف در جهت ارتقای خواص مکانیکی خود بهره میبرند. الیاف تقویتی بر اساس قطر و مشخصاتشان به سه دسته ویسکر، رشته و سیم تقسیم میشوند. خواص نهایی این کامپوزیتها تابعی از خواص رشته، میزان نیروی منتقل شده از فاز ماتریس و درصد حجمی آن است. نکته حائز اهمیت این است که در FRCها، با کاهش قطر رشته، شاهد افزایش استحکام نهایی خواهیم بود.
2- کامپوزیتهای تقویت شده با ذرات (PRC)
کامپوزیتهای تقویت شده با ذرات (PRC) نوعی از مواد کامپوزیتی هستند که از ذرات ریز و پراکنده به عنوان عامل تقویت کننده در یک ماده زمینه استفاده میکنند. این ذرات میتوانند سرامیکی، فلزی یا غیرآلی باشند و به طور یکنواخت در سرتاسر ماده زمینه توزیع میشوند. بر اساس مکانیزم تقویت، کامپوزیتهای PRC به دو دسته کامپوزیتهای درشت ذره و کامپوزیتهای مستحکم شده با ذرات پراکنده تقسیم میشوند.
کامپوزیتهای درشتذره
در کامپوزیتهای درشتذره، اندازه ذرات تقویتکننده بزرگتر از 100 نانومتر است. به همین دلیل، فعل و انفعال بین ذره و ماتریس در سطح مولکولی یا اتمی رخ نمیدهد. در عوض، ذرات تقویتکننده مانند سدی در برابر حرکت ماتریس عمل میکنند و از تغییر شکل آن در هنگام اعمال تنش جلوگیری میکنند. این مکانیزم باعث افزایش استحکام و سختی کامپوزیت میشود.
کامپوزیتهای سبز
این کامپوزیتها از نظر زیستمحیطی بسیار پایدار هستند چرا که از موادی ساخته شدهاند که به طور طبیعی در محیط زیست تجزیه میشوند. فاز زمینه این نوع کامپوزیت از پلیمرهای سنتزی قابل جذب بیولوژیکی و فاز تقویتکننده آن از الیاف گیاهی تشکیل شده است. به این ترتیب، پس از پایان عمر مفید این مواد، به جای ماندن در محیط زیست، به طور کامل در چرخه زیستی کره زمین جذب میشوند.
خواص مکانیکی، شیمیایی و الکتریکی کامپوزیتها
کامپوزیتها، با ترکیب مواد مختلف، میتوانند نقاط ضعف هریک را جبران، نقاط قوت را تقویت و ویژگیهای جدیدی ایجاد کنند. خواص نهایی، به عواملی مانند نسبت، اندازه و شکل مواد تقویتکننده، نحوه توزیع آنها، خواص مکانیکی ماتریس و نوع اتصال بین ماتریس و تقویتکننده بستگی دارد. از جمله مهمترین این خواص میتوان به موارد زیر اشاره کرد:
1- مقاومت در برابر خوردگی: در برابر مواد خورنده و شیمیایی، آب، رطوبت و تابش نور مقاوم هستند.
2- مقاومت مکانیکی: میتوان آنها را به گونهای طراحی کرد که در جهت خاص، استحکام بیشتری داشته باشند.
3- مقاومت الکتریکی: بسته به نوع مواد، عایق یا هادی هستند.
4- مقاومت در برابر خستگی: به ویژه کامپوزیتهای الیاف، در برابر ترک و تنش مقاوم هستند.
5- مقاومت در برابر شکستگی: در برابر شکستگی ناگهانی مقاوم هستند.
6- میرایی خوب
7- چگالی پایین
8- سهولت در تولید و ساخت شکلهای پیچیده، با روشهای ساده، کارآمد و مقرون به صرفه
9- آسان بودن مونتاژ قطعات و عملیات تعمیر و عیبیابی
10- ضریب انبساط حرارتی پایین
11- بهبود اتصالات و تولید یکپارچه
12- جذب انرژی مناسب
سخن آخر
این مقاله به بررسی ساختار، خواص و انواع مختلف کامپوزیتها پرداخته و سهم بسزای این مواد در صنایع مختلف را به ویژه در صنایعی که نیازمند تلفیقی از خواص مختلف هستند، تاکید میکند. پیشرفتهای چشمگیر در فناوری ساخت کامپوزیتهای پلیمری، طیف گستردهای از کاربردها را برای این مواد ارزشمند به ارمغان آورده است.
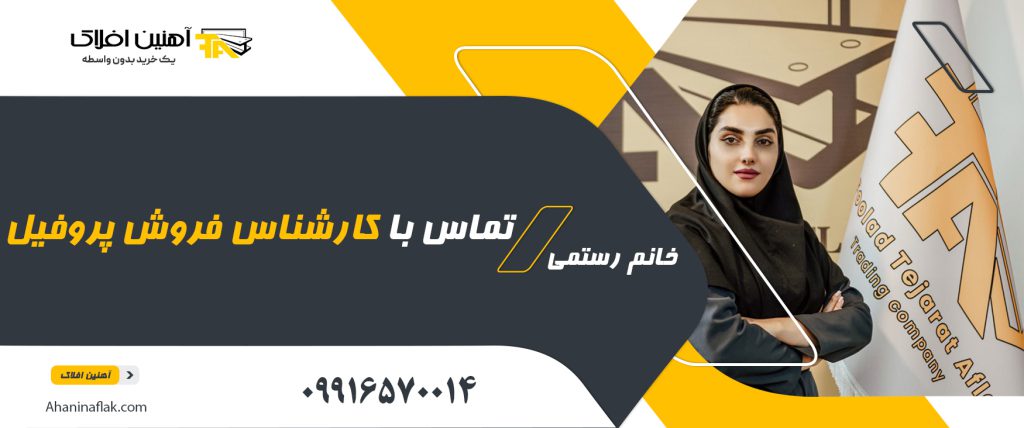